3D Printing Materials
Prototyping plastics, printed on FDM printers, are ideal for designers and engineers to cost-effectively produce and test a design. Rapid low cost prototyping allows for more design iterations resulting in greater control over the design process and improved end products.
Strengths
-
Rapid turnaround time
-
Inexpensive
-
Form and fit prototyping
Limitations
-
Overhangs require support which will affect surface finish
-
Print layers are visible
-
Anisotropic (weak in the Z direction)
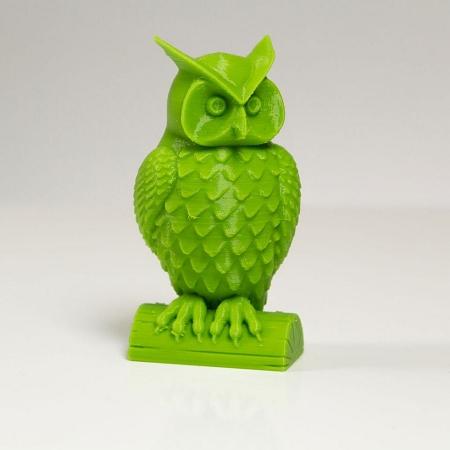

UV-cured resin prints display fine details, sharp edges and a smooth finish. Color availability is limited, but it is easily paintable and can also be semi-translucent. High Detail Resin is ideal for printing intricate designs and sculptures, as up to 0.2mm is enough to create clearly visible details. Apart from size, resin comes with hardly any design restrictions.
Strengths
-
Intricate designs and sculptures
-
Small, high detail models
-
Jewelry, art
-
Investment casting
Limitations
-
Large models
-
Extensive exposure to UV-light
SLS (Selective Laser Sintering) uses a laser to shape and form extremely thin layers of powdered material by melting it together one-by-one to create a solid structure. The advantage of this process is that the excess unmelted powder acts as a support to the structure as it is being produced which allows for complex shapes to be made and no additional supports are required.
Strengths
-
Functional prototypes and end products
-
Complex designs with intricate details
-
Moving and assembled parts
-
Cases, holders, adapters
Limitations
-
Cavities within design (unless making use of escape holes)


Fiber-Reinforced Nylon materials are designed to print parts with the strength of metal. Thanks to Markforged’s continuous fiber fabrication process, you can now 3D print parts with a higher strength-to-weight ratio than 6061-T6 Aluminum, up to 27x stiffer and 24x stronger than ABS.
Strengths
-
Engineering parts
-
Custom end-use production parts
-
Functional prototyping and testing
-
Structural parts
-
Jigs, fixtures and other tooling
Limitations
-
Small parts with intricate details
Rigid Opaque Plastic (Vero) is the go-to material for realistic prototypes, providing excellent details, high accuracy and smooth surface finish with up to 16 micron layer heights. With Rigid Opaque Plastic, you can 3D print attractive prototypes that closely resemble the ‘look’ of the end product and test fit, form and function, even for moving and assembled parts.
Strengths
-
Fine-detail models with smooth surfaces
-
Form and fit testing
-
Sales, marketing and exhibition models
-
Moving and assembled parts
Limitations
-
End products (sensitive to UV light)

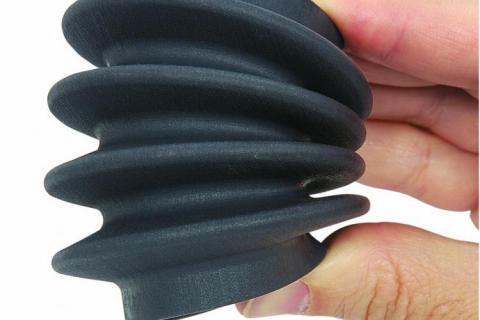
With Rubber-Like Plastic (Tango), you can simulate rubber with various levels of elastomer characteristics including Shore Scale A hardness, elongation at break, tear resistance and tensile strength. This material enables you to simulate a wide variety of finished products, such as non-slip or soft surfaces on consumer electronics, medical devices and automotive interiors.
Strengths
-
Detailed models with various level of flexibility (Shore A 27 to 95)
-
Soft-touch coatings, grips or nonslip surfaces
-
Fine details and smooth surfaces
-
Over-molding solid objects with rubber-like surroundings
Limitations
-
End products (sensitive to UV light)
Transparent plastic is one of the clearest 3D printing materials available; combining clarity with high precision and smooth surface finish. This material is ideal for form and fit testing of see-through parts, fine-detail model building, enabling you to prototype clear and tinted products from eyewear and lighting covers to medical devices.
Strengths
-
Form and fit testing of see-through parts like: glass consumer products, eyewear, lighting covers and cases
-
Fine-detail models with smooth surfaces
-
Sales, marketing and exhibition models
-
Medical or scientific visualizations
Limitations
-
End products (sensitive to UV light)


Simulated ABS is designed to imitate ABS engineering plastics by combining strength with high-temperature resistance. It provides high impact resistance and shock absorption along with a beautiful smooth surface finish. With Simulated ABS, you can create high precision engineering tools as well as tough and durable prototypes. It is the fastest and most affordable way to produce high precision injection molds for small injection molding runs of 10-100 pieces.
Strengths
-
Molds, including injection molds
-
Tough and heat resistant prototypes
-
Fine-detail models with smooth surfaces
-
Form, fit, and functional testing
Limitations
-
End products (sensitive to UV light)
Gypsum with a colored texture on the surface. The best choice for photo-realistic, full color prints. Ideal for professional (scale) models, architecture, product design and fine arts. Full Color Sandstone doesn’t allow for protruding features smaller than 3 millimeters because of the brittleness of the material. Also walls have to be wider than 2 millimeters.
Strengths
-
Architectural models
-
Lifelike sculptures
-
Gifts and memorabilia
-
Complex models
Limitations
-
Functional parts
-
Intricate features


Direct metal 3D printing allows you to create functional prototypes and mechanical parts from various metals and alloys. Industrial metals are laser sintered from metal powder. Available materials include aluminum, stainless steel, bronze and cobalt chromium.
Strengths
-
Functional prototypes and end-use parts
-
Complex designs with intricate details
-
Mechanical parts
-
Moving and assembled parts
Limitations
-
Cavities within design (unless making use of escape holes)